Aluminium oxide grinding presents unique challenges and opportunities in the realm of industrial applications. As an essential material in manufacturing and refining processes, aluminium oxide is valued for its hardness, thermal stability, and resistance to corrosion. To understand its optimal application in grinding, it’s crucial to explore experiences from the field, expert insights, authoritative guidelines, and establish the credibility of information provided.
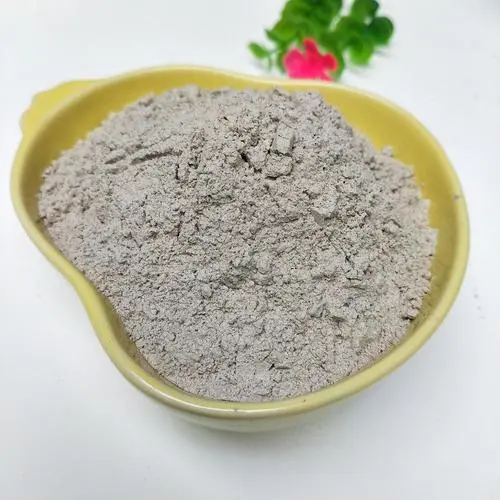
Aluminium oxide's use in grinding is rooted in its characteristic hardness, which makes it an ideal abrasive for cutting tools. This abrasive quality helps in achieving precise material removal from a workpiece with consistency and efficiency. The grains of aluminium oxide are utilized in various forms – bonded abrasives, coated abrasives, and loose grain abrasives. Each form has specific applications, depending on the desired finish and the type of material being worked on.
Expertise in working with aluminium oxide grinding indicates the critical influence of selecting the right grain size and bonding matrix. The performance and service life of the abrasive wheel are impacted significantly by these parameters. For instance, larger grain sizes are typically used for rapid material removal, while finer grains are employed for finishing operations that require a high degree of precision and finer surface finishes.
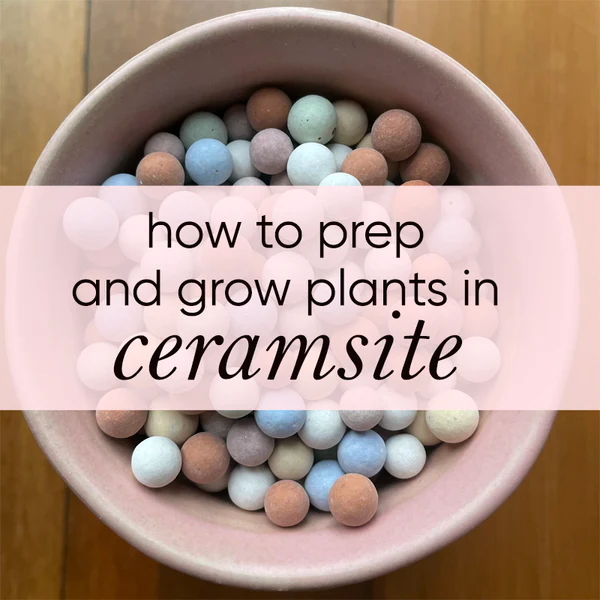
Professionals in the field advocate for understanding the cooling and lubrication requirements during aluminium oxide grinding. Uneven heating or insufficient lubrication can lead to thermal damage to the workpiece and reduced lifespan of the grinding wheel. The introduction of coolant is essential to reduce heat buildup, ensuring both the quality of the grinding process and the longevity of the equipment used.
Establishing authority on the subject, several industry standards such as the ANSI and ISO provide guidelines on safe and efficient use of aluminium oxide in grinding processes. These standards underscore the importance of personal protective equipment (PPE), machine guarding, and regular maintenance checks to prevent accidents and prolong the life of grinding equipment.
aluminium oxide grinding
Trust in aluminium oxide grinding processes is augmented through research and development by leading manufacturers. Companies like Saint-Gobain Abrasives and 3M invest heavily in innovation to refine the properties of aluminium oxide abrasives. Their research endeavors aim to enhance the performance, safety, and sustainability of aluminium oxide products, making them more reliable in various industrial settings.
In practical application, user experiences convey that while aluminium oxide abrasives are suitable for a wide range of materials, including metals, wood, and ceramics, there are nuances in their use. For example, when grinding ferrous metals, aluminium oxide performs well due to its durability. However, its performance can vary when used with non-ferrous metals like aluminum, where softer abrasives might be needed to prevent heat buildup and material clogging.
Workers employing aluminium oxide abrasive solutions often share real-world insights into process optimization. Strategies include adjusting wheel speed to accommodate different materials, regular dressing of the grinding wheel to maintain its sharpness, and periodic checks for wear and tear.
Aluminium oxide’s reputation as a versatile, robust grinding solution is further evidenced by its widespread use across multiple industries – from aerospace and automotive to electronics and construction. In each sector, the material’s consistent performance in achieving desired surface finishes while maintaining process efficiency exemplifies its trusted role in industrial operations.
The convergence of empirical experiences, expert knowledge, adherence to authoritative guidelines, and an enduring trust in its capabilities positions aluminium oxide grinding as an indispensable tool in modern manufacturing processes. This comprehensive understanding not only facilitates improved operational outcomes but also ensures a safer, more sustainable approach to grinding challenges.